“Beyond the Basics: Understanding the 2 Bar GM Map Sensors and Their Crucial Role in Vehicle Performance”- 2023
Introduction
Unraveling the Mystery Behind the 2 Bar GM Map Sensor
In the intricate world of automotive engineering, a myriad of sensors play crucial roles in optimizing engine performance and ensuring seamless operation. Among these, the 2 Bar GM Map Sensor stands out as a critical component, silently monitoring and regulating key parameters that govern engine efficiency and power output.
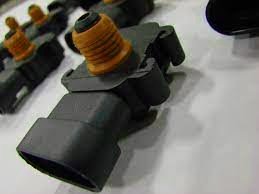
Technical Specifications – 2 Bar GM Map Sensors
Voltage Range and Pressure Sensitivity
The 2 Bar GM Map Sensors boasts an impressive voltage output range of 0.6V to 4.9V, corresponding to a pressure range of 40kPa to 204kPa. This wide operating range allows the sensor to accurately measure and respond to a vast spectrum of intake manifold pressures, catering to the demands of both naturally aspirated and forced-induction engines.
Precision and Accuracy
The 2 Bar GM Map Sensors are renowned for its exceptional precision and accuracy. Its sensitivity to minute pressure changes ensures that the ECU receives precise MAP data, enabling it to make finely tuned adjustments to fuel injection and ignition timing. This high level of precision translates into optimized engine performance and fuel economy.
Distinct Features
The 2 Bar GM Map Sensors distinguishes itself from its counterparts through its unique combination of features:
High Pressure Range: Capable of accurately measuring boost pressure up to 14.5psi, making it ideal for forced-induction applications.
Linear Output: Produces a linear voltage output over its entire operating range, ensuring accurate data interpretation by the ECU.
Environmental Durability: Built to withstand the harsh conditions of the engine bay, including extreme temperatures and vibrations.
Plug-and-Play Design: Seamlessly integrates with existing GM-style MAP sensor connectors, simplifying installation and maintenance.
Benefits to the Automotive Table
The 2 Bar GM Map Sensors brings a plethora of benefits to the automotive landscape: Optimizes Engine Performance: Provides real-time MAP data, enabling the ECU to adjust fuel injection and ignition timing for optimal combustion efficiency and power output.
Enhances Fuel Economy: Accurate MAP readings contribute to efficient fuel utilization, reducing fuel consumption and extending driving range.
Reduces Emissions: By optimizing air-fuel mixture and combustion, the sensor helps minimize harmful emissions, promoting cleaner and more environmentally friendly operation.
Improves Acceleration and Power Delivery: Accurate MAP data ensures smooth and responsive acceleration, delivering a more enjoyable driving experience.
Increases Boost Pressure Accuracy: In forced-induction applications, the sensor’s high pressure range allows for precise boost pressure monitoring and control, maximizing power output.
The Inner Workings
Sensor Anatomy
The 2 Bar GM Map Sensors are marvel of engineering, its compact size housing a sophisticated array of components that work in harmony to deliver accurate MAP readings.
Key Components:
Sensing Diaphragm: A thin, flexible membrane that deflects in response to changes in air pressure.
Piezoresistive Element: A semiconductor material attached to the diaphragm, its electrical resistance changing as the diaphragm deflects.
Signal Conditioning Circuit: An electronic circuit that amplifies and converts the resistance changes into a voltage output.
Housing: A protective enclosure that shields the sensor’s internal components from external elements.
Electrical Connector: A connector that provides the interface for transmitting the voltage signal to the ECU.
Decoding the Significance of Each Component:
Sensing Diaphragm: The pressure-sensitive element that directly translates pressure changes into mechanical deflections.
Piezoresistive Element: The heart of the sensor, converting mechanical deflections into electrical signals.
Signal Conditioning Circuit: The intermediary, transforming the resistance changes into a usable voltage signal.
Housing: The guardian, shielding the delicate internal components from environmental hazards.
Electrical Connector: The communication channel, relaying the sensor’s vital information to the ECU.
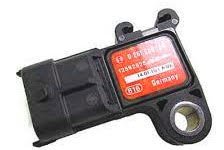
How It Operates – 2 Bar GM Map Sensors
A Dance Between Pressure and Voltage
The 2 Bar GM Map Sensors operates on the principle of piezoresistive transduction, a captivating interplay between mechanical force and electrical resistance.
Pressure Application: Changes in air pressure within the intake manifold exert force on the sensing diaphragm.
Diaphragm Deflection: The diaphragm deflects accordingly, altering the physical strain on the piezoresistive element.
Resistance Change: The strain induces a corresponding change in the electrical resistance of the piezoresistive element.
Signal Amplification: The signal conditioning circuit amplifies the minute resistance change into a measurable voltage signal.
Voltage Output: The voltage signal, proportional to the applied pressure, is transmitted to the ECU for interpretation.
Sensor Response under Varying Conditions
The 2 Bar GM Map Sensor exhibits remarkable responsiveness across a wide range of intake manifold pressures:
Low Pressure: At low pressures, the diaphragm deflects minimally, producing a low voltage output.
High Pressure: As pressure increases, the diaphragm deflects more significantly, generating a higher voltage output.
Linearity: The voltage output maintains a linear relationship with the applied pressure, ensuring accurate MAP readings across its operating range.
The sensor’s ability to accurately translate pressure changes into voltage signals is the foundation for its role in optimizing engine performance and fuel economy.
Evolution of Automotive Sensors
The Dawn of MAP Sensors
The genesis of 2 Bar GM Map Sensors can be traced back to the 1970s, a period marked by advancements in electronic engine management systems. As fuel injection and ignition timing became computer-controlled, the need for precise air intake measurement emerged. Early MAP sensors, utilizing mechanical diaphragms and variable resistors, laid the groundwork for the sophisticated sensors we know today.
Milestones Leading to the 2 Bar GM Map Sensors
The evolution of 2 Bar GM Map Sensors has been punctuated by a series of technological milestones:
Solid-State Sensors: The introduction of solid-state piezoresistive sensors in the 1980s marked a significant leap forward, offering improved accuracy, reliability, and compactness.
Digitalization: The advent of digital signal processing in the 1990s enabled more precise and efficient data interpretation, enhancing the overall performance of MAP sensors.
Integration with Engine Management Systems: Seamless integration with engine control units (ECUs) became a hallmark of MAP sensors in the 2000s, allowing for real-time adjustments to engine parameters.
The 2 Bar GM Map Sensors: A Culmination of Innovation
The 2 Bar GM Map Sensor represents the culmination of decades of research and development in MAP sensor technology. Its advanced features, such as high pressure range, linear output, and environmental durability, reflect the continuous pursuit of improved engine performance and fuel efficiency in modern automotive engineering.
Technological Advancements
The Ever-Evolving Landscape of Sensor Technology
The quest for enhanced sensor performance continues to drive innovation in MAP sensor technology:
Microelectromechanical Systems (MEMS): MEMS technology is revolutionizing sensor design, enabling smaller, more robust, and more accurate sensors.
Wireless Communication: Wireless sensor networks are paving the way for real-time data exchange and remote monitoring of engine performance.
Artificial Intelligence (AI): AI algorithms are being explored to enhance sensor data interpretation and optimize engine control strategies.
Future Prospects of MAP Sensors in the Automotive Realm
As the automotive industry embraces electrification, connectivity, and autonomous driving, MAP sensors remain indispensable components:
Electric Vehicles (EVs): MAP sensors play a crucial role in optimizing battery usage and regenerative braking in EVs.
Connected Cars: MAP sensor data can be integrated into advanced driver-assistance systems (ADAS) and vehicle-to-everything (V2X) communication protocols.
Autonomous Vehicles: Precise MAP data is essential for autonomous vehicles to make informed decisions and navigate complex environments safely.
The future of MAP sensors holds immense promise, with advancements in materials science, manufacturing processes, and data analytics poised to further enhance their performance, reliability, and integration into the automotive landscape.
Challenges and Solutions
Environmental Factors
The 2 Bar GM Map Sensors, like any electronic device, can be affected by external environmental factors. While its robust design and construction make it well-suited for the harsh conditions of the engine bay, certain factors warrant consideration:
Temperature Extremes: Extreme temperatures, both hot and cold, can impact the sensor’s performance. Excessive heat can cause the sensing diaphragm to warp or the piezoresistive element to become less responsive. Conversely, extreme cold can stiffen the diaphragm and reduce its sensitivity to pressure changes.
Vibrations: The engine bay is a dynamic environment, and constant vibrations can potentially affect the sensor’s internal components. Over time, vibrations can lead to loose connections or damage to delicate components.
Moisture and Contaminants: Moisture and contaminants, such as dust and debris, can infiltrate the sensor’s housing, potentially causing corrosion or interference with the electrical components.
Solutions and Adaptations for Challenging Environments
To mitigate the impact of environmental factors, several solutions and adaptations can be employed:
Protective Housing: The sensor’s housing should be designed to withstand extreme temperatures and vibrations. Additionally, protective seals can prevent moisture and contaminants from entering the housing.
Material Selection: The choice of materials for the sensor’s internal components is crucial. High-quality materials with low thermal expansion coefficients can minimize the effects of temperature variations.
Vibration Dampening: Vibration dampening mounts or gaskets can be incorporated into the sensor’s mounting system to reduce the transmission of vibrations.
Regular Maintenance: Regular inspection and cleaning of the sensor and its surroundings can help prevent the buildup of debris and moisture that could compromise performance.
FAQS
What is the 2 Bar GM Map Sensor?
The 2 Bar GM Map Sensor, also known as the Manifold Absolute Pressure Sensor, is an electronic device that measures the air pressure within the intake manifold of an engine. This pressure reading, known as manifold absolute pressure (MAP), serves as a crucial indicator of engine load.
Why is the 2 Bar GM Map Sensor Important?
The 2 Bar GM Map Sensor plays a pivotal role in engine performance by providing real-time information about the engine’s air consumption and demand. This information is relayed to the engine control unit (ECU), which then adjusts fuel injection and ignition timing accordingly, ensuring optimal air-fuel mixture and combustion efficiency.
How Does the 2 Bar GM Map Sensor Work?
The 2 Bar GM Map Sensor works by using a method called piezoresistive transduction. As the air pressure increases in the intake manifold, it causes the sensor’s diaphragm to move, which alters the electrical resistance. This change in resistance is then converted into a voltage signal and sent to the ECU (Engine Control Unit).
What Applications Does the 2 Bar GM Map Sensor Have?
The 2 Bar GM Map Sensor is primarily used in forced-induction engines, such as those equipped with turbochargers or superchargers. These engines generate significant boost pressure, which can exceed the measurement range of a standard MAP sensor. The 2 Bar GM Map Sensor, with its higher pressure range, can accurately monitor and regulate boost pressure, ensuring optimal engine performance.
Conclusion
The 2 Bar GM Map Sensors stands as a testament to the remarkable advancements in automotive technology, seamlessly integrating advanced sensing capabilities with sophisticated engine management systems. Its role in optimizing engine performance and ensuring efficient operation is undeniable, making it an indispensable component in the realm of modern automotive engineering.